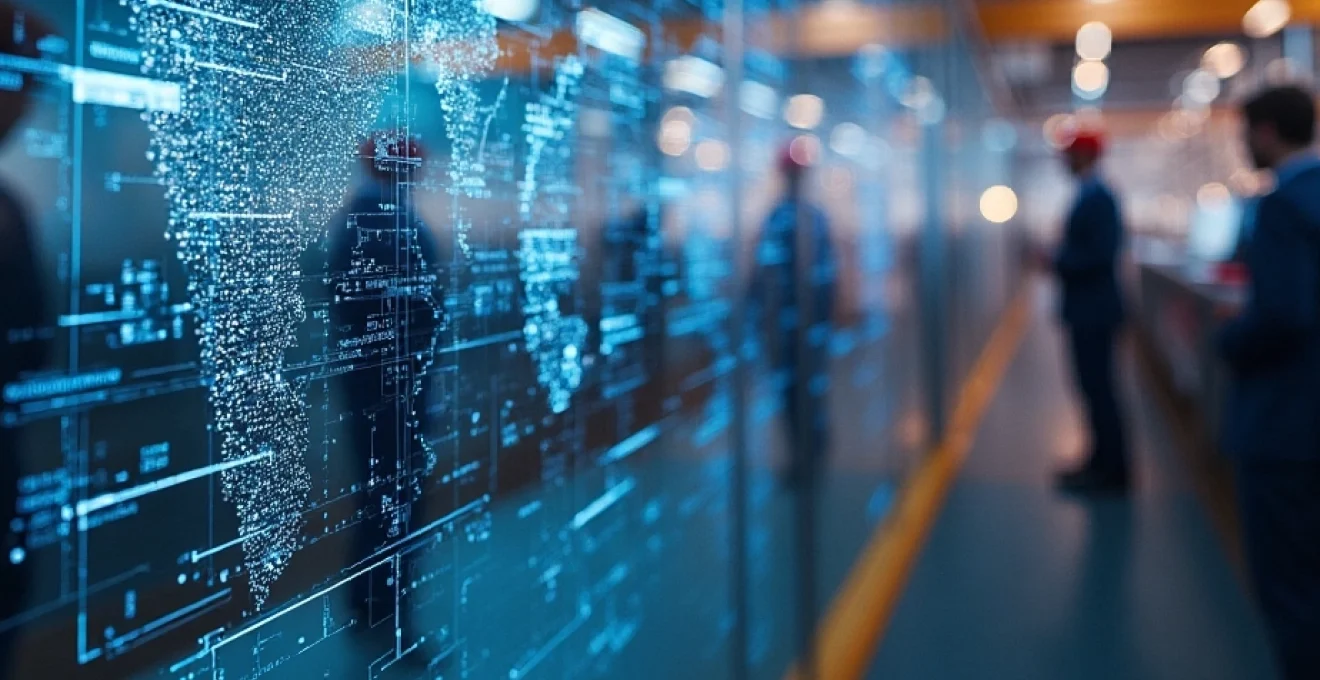
The world is on the cusp of a profound transformation as we enter the era of the Fourth Industrial Revolution. This seismic shift is characterized by the convergence of cutting-edge technologies that are blurring the lines between physical, digital, and biological spheres. At the heart of this revolution lies innovation technology, which is propelling industries forward at an unprecedented pace. From artificial intelligence and the Internet of Things to advanced robotics and quantum computing, these technologies are not just enhancing existing processes but fundamentally reshaping how we produce, consume, and interact with the world around us.
As we delve into the intricacies of this technological renaissance, it becomes clear that the impact of these innovations extends far beyond the factory floor. They are revolutionizing supply chains, transforming energy production, and even altering the very fabric of our economic systems. The Fourth Industrial Revolution promises to bring about changes that are not just incremental but exponential, offering solutions to some of humanity’s most pressing challenges while simultaneously presenting new questions about the future of work, privacy, and societal structures.
Industry 4.0: convergence of AI, IoT, and robotics
Industry 4.0 represents the pinnacle of modern manufacturing, where smart factories leverage the power of artificial intelligence (AI), the Internet of Things (IoT), and advanced robotics to create highly efficient and flexible production systems. This convergence is creating a new paradigm in industrial operations, where machines communicate with each other, make autonomous decisions, and continuously optimize processes without human intervention.
At the core of Industry 4.0 is the concept of cyber-physical systems, where the physical world is seamlessly integrated with digital technologies. Sensors embedded throughout the production line collect vast amounts of data, which is then analyzed in real-time by AI algorithms to predict maintenance needs, adjust production schedules, and even customize products on the fly. This level of interconnectedness and intelligence is transforming manufacturing from a linear process to a dynamic, responsive ecosystem.
The impact of this convergence extends beyond efficiency gains. It’s enabling manufacturers to respond more quickly to market demands, reduce waste, and create personalized products at scale. For instance, automotive companies are now able to offer an unprecedented level of customization, allowing customers to design their vehicles with a myriad of options, all thanks to the flexibility afforded by smart manufacturing systems.
Industry 4.0 is not just about technology; it’s about reimagining the entire manufacturing value chain to create more value for customers and stakeholders.
Advanced manufacturing technologies reshaping production
The landscape of manufacturing is being dramatically reshaped by a suite of advanced technologies that are pushing the boundaries of what’s possible in production. These innovations are not only enhancing efficiency and quality but also opening up new possibilities for product design and customization. Let’s explore some of the key technologies that are at the forefront of this manufacturing revolution.
Additive manufacturing and 3D printing revolution
Additive manufacturing, commonly known as 3D printing, has evolved from a prototyping tool to a full-fledged production technology. This process of building objects layer by layer is revolutionizing manufacturing by enabling the creation of complex geometries that were previously impossible or prohibitively expensive to produce using traditional methods. Industries from aerospace to healthcare are leveraging 3D printing to create lightweight components, personalized medical implants, and even entire buildings.
The flexibility of 3D printing is also transforming supply chains. Companies can now produce spare parts on-demand, reducing inventory costs and lead times. Moreover, the ability to print objects at the point of use is decentralizing manufacturing, potentially reshaping global trade patterns and reducing the carbon footprint associated with shipping goods across long distances.
Smart factories and digital twin concept
The concept of the digital twin is revolutionizing how products are designed, manufactured, and maintained. A digital twin is a virtual replica of a physical product or process, updated in real-time with data from sensors on its physical counterpart. Siemens has been at the forefront of implementing this technology, creating digital twins of entire factories to optimize operations and predict maintenance needs before they occur.
In a Siemens smart factory, every aspect of the production process is simulated in the digital realm. This allows engineers to test changes and optimizations virtually before implementing them in the physical world, significantly reducing downtime and improving efficiency. The digital twin concept is not limited to manufacturing; it’s being applied to everything from urban planning to healthcare, offering a new way to understand and interact with complex systems.
Nanotechnology in materials science and engineering
Nanotechnology is pushing the boundaries of materials science, enabling the creation of materials with properties that were once thought impossible. By manipulating matter at the atomic and molecular scale, scientists and engineers are developing materials that are stronger, lighter, and more versatile than their conventional counterparts. These nanomaterials are finding applications across industries, from ultra-strong and lightweight composites for aerospace to self-cleaning surfaces for consumer products.
In the realm of energy, nanotechnology is paving the way for more efficient solar cells and energy storage devices. Nanomaterials are enhancing the performance of batteries, potentially revolutionizing electric vehicles and renewable energy storage. The impact of nanotechnology on manufacturing is profound, as it enables the creation of products with enhanced functionality and performance, opening up new markets and applications.
Autonomous systems and cobots in assembly lines
The integration of autonomous systems and collaborative robots (cobots) is transforming assembly lines, making them more flexible and efficient. Unlike traditional industrial robots that operate in isolation, cobots are designed to work alongside humans, combining the precision and strength of machines with the problem-solving skills and adaptability of human workers.
These intelligent machines are equipped with advanced sensors and AI algorithms that allow them to perceive their environment and make decisions in real-time. They can adapt to changes in the production line, handle delicate tasks, and even learn new skills through machine learning techniques. The result is a more agile manufacturing process that can quickly adapt to changing product designs or market demands.
Cobots are particularly valuable in industries where complete automation is challenging or undesirable. They’re being used in everything from automotive assembly to electronics manufacturing, enhancing productivity while also improving workplace safety by taking on hazardous or repetitive tasks.
Blockchain and distributed ledger technologies in supply chains
Blockchain and distributed ledger technologies (DLT) are poised to revolutionize supply chain management, offering unprecedented levels of transparency, traceability, and security. These technologies create an immutable record of transactions across a network of computers, eliminating the need for intermediaries and reducing the risk of fraud or data tampering.
In the context of supply chains, blockchain enables real-time tracking of goods from the point of origin to the end consumer. This level of visibility is particularly valuable in industries where provenance is critical, such as food safety or luxury goods. For example, retailers can use blockchain to verify the authenticity of products and ensure they were sourced ethically, while consumers can access detailed information about the journey of their purchases.
Moreover, smart contracts built on blockchain platforms are automating and streamlining supply chain processes. These self-executing contracts can automatically trigger payments, update inventory levels, and initiate new orders based on predefined conditions, reducing administrative overhead and minimizing errors.
Blockchain in supply chains is not just about efficiency; it’s about creating trust and accountability in an increasingly complex global trade network.
Quantum computing: accelerating industrial problem-solving
Quantum computing represents a paradigm shift in computational power, with the potential to solve complex industrial problems that are beyond the reach of classical computers. Unlike traditional bits that can only be in a state of 0 or 1, quantum bits or qubits can exist in multiple states simultaneously, allowing quantum computers to perform certain calculations exponentially faster than their classical counterparts.
IBM’s quantum advantage in chemical simulations
IBM has been at the forefront of quantum computing research, demonstrating the technology’s potential in areas such as chemical simulations. Quantum computers are particularly well-suited for modeling molecular interactions, which could accelerate drug discovery and the development of new materials. IBM’s quantum systems have shown promise in simulating complex chemical reactions with a level of accuracy that would take classical computers years to achieve.
This quantum advantage in chemical simulations could have far-reaching implications for industries ranging from pharmaceuticals to energy. For instance, it could lead to the discovery of more efficient catalysts for industrial processes or help in the design of new drugs tailored to specific genetic profiles.
D-Wave systems’ quantum annealing for optimization
D-Wave Systems has taken a different approach to quantum computing, focusing on quantum annealing to solve optimization problems. This technique is particularly useful for finding the best solution among a vast number of possibilities, which is common in logistics, financial modeling, and machine learning.
Several industries are already exploring the potential of D-Wave’s quantum annealing systems. For example, automotive manufacturers are using quantum annealing to optimize traffic flow in smart cities, while financial institutions are leveraging it to improve portfolio optimization and risk analysis.
Google’s sycamore processor and quantum supremacy
Google made headlines with its claim of achieving quantum supremacy using its Sycamore processor. Quantum supremacy refers to the point at which a quantum computer can perform a calculation that would be practically impossible for a classical computer. While the specific problem solved by Sycamore was highly specialized, it marked a significant milestone in the field of quantum computing.
The implications of Google’s achievement extend beyond academic interest. It suggests that we are approaching a point where quantum computers could start to tackle real-world problems that have long been considered intractable. This could lead to breakthroughs in areas such as climate modeling, cryptography, and artificial intelligence.
Post-quantum cryptography for industrial security
As quantum computing advances, there is growing concern about its potential to break current encryption methods. This has led to the development of post-quantum cryptography, which aims to create encryption algorithms that are secure against both classical and quantum computers.
Industries that rely on long-term data security, such as banking and defense, are already investing in post-quantum cryptography to future-proof their systems. The National Institute of Standards and Technology (NIST) is leading efforts to standardize post-quantum cryptographic algorithms, ensuring that critical infrastructure remains secure in the quantum era.
Sustainable energy technologies driving industrial transformation
The transition to sustainable energy sources is not just an environmental imperative; it’s becoming a key driver of industrial innovation and competitiveness. Renewable energy technologies, coupled with advanced energy storage systems and smart grids, are reshaping the industrial landscape and opening up new opportunities for efficiency and sustainability.
Solar and wind power have seen dramatic cost reductions and efficiency improvements, making them increasingly viable for industrial applications. Many manufacturing facilities are now integrating on-site renewable energy generation, reducing their reliance on the grid and lowering their carbon footprint. This shift is not only reducing operational costs but also providing a hedge against energy price volatility.
Advanced energy storage technologies, particularly lithium-ion batteries and emerging alternatives like solid-state batteries, are enabling industries to better manage intermittent renewable energy sources. These storage systems allow factories to store excess energy generated during peak production times and use it during periods of high demand or low renewable output.
Moreover, the concept of the circular economy is gaining traction, with industries looking for ways to reuse and recycle materials and energy. This approach is leading to innovations in waste heat recovery, where excess heat from industrial processes is captured and used for other purposes, such as district heating or electricity generation.
Edge computing and 5G networks enhancing industrial IoT
The convergence of edge computing and 5G networks is set to supercharge the Industrial Internet of Things (IIoT), enabling faster data processing, reduced latency, and more robust connectivity. This combination is critical for realizing the full potential of smart factories and autonomous systems.
Real-time analytics with fog computing architecture
Fog computing, an extension of edge computing, brings data processing closer to the source of data generation. In industrial settings, this means that critical decisions can be made in real-time, without the need to send data to a centralized cloud for processing. This architecture is particularly valuable in scenarios where milliseconds matter, such as in autonomous vehicle systems or industrial safety applications.
By distributing computing resources throughout the network, fog computing enables more efficient use of bandwidth and reduces the strain on central data centers. It also enhances data security by minimizing the amount of sensitive information that needs to be transmitted over long distances.
Predictive maintenance using machine learning at the edge
One of the most promising applications of edge computing in industry is predictive maintenance. By processing sensor data from machinery at the edge, AI algorithms can detect anomalies and predict potential failures before they occur. This approach significantly reduces downtime and maintenance costs, as repairs can be scheduled proactively during planned production breaks.
Machine learning models deployed at the edge can continuously learn and adapt to new patterns, improving their accuracy over time. This dynamic approach to maintenance is particularly valuable in complex manufacturing environments where conditions can change rapidly.
Low-latency control systems for critical operations
The combination of edge computing and 5G networks enables ultra-low-latency control systems for critical industrial operations. In industries such as robotics or precision manufacturing, where split-second timing is crucial, these technologies allow for near-instantaneous communication between sensors, controllers, and actuators.
This capability is opening up new possibilities for remote operations and telerobotics. For instance, surgeons can now perform delicate procedures using robotic systems controlled over 5G networks, with the low latency ensuring precise and timely response to their movements.
Industrial AR/VR applications powered by edge computing
Augmented Reality (AR) and Virtual Reality (VR) are finding increasing applications in industrial settings, from training and maintenance to design and quality control. Edge computing plays a crucial role in making these applications viable by processing the vast amounts of data required for immersive experiences locally, reducing latency and improving user experience.
For example, maintenance technicians can use AR headsets to access real-time information about equipment they’re working on, with the edge infrastructure processing sensor data and overlaying relevant information in their field of view. This not only improves efficiency but also reduces the risk of errors in complex maintenance procedures.
As we look to the future, it’s clear that innovation technology will continue to drive the next industrial revolution, reshaping not just how we produce goods but how we interact with the world around us. From quantum computing solving previously intractable problems to sustainable energy technologies powering a new era of clean industry, the possibilities are as exciting as they are transformative. The challenge now lies in harnessing these technologies responsibly, ensuring that the benefits of this revolution are widely shared and that we address the ethical and societal implications that come with such profound change.